
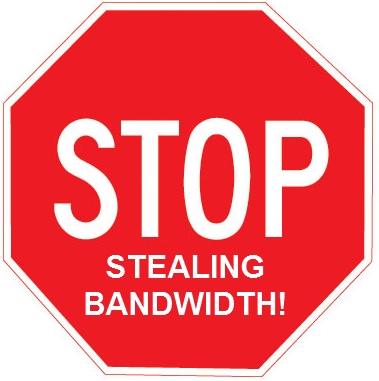
leon
Members-
Posts
28 -
Joined
-
Last visited
Content Type
Profiles
Articles
Forums
Gallery
Everything posted by leon
-
2017 F-Series 6.7L A/C Not Cooling
leon replied to Keith Browning's topic in Body, Chassis and Electrical
"but like my original post, remove the convolute from the clutch coil harness take out and give both wires a good tug. Just to be sure. " (Keith Browning) I did and I did find the ground circuit broke at one of the zip ties, they were really squeezed tight and I went so far as to go back in the harness as far as I could and cut out the power and ground circuits to my coil, and installed about 7 " good wire performed wiggle test again and all good. You told me twice, I knew you meant business. Thanks for that. -
2017 F-Series 6.7L A/C Not Cooling
leon replied to Keith Browning's topic in Body, Chassis and Electrical
I did not identify the Freon...our dealer, uhm, well, we don't have one. We need to get one. -
2017 F-Series 6.7L A/C Not Cooling
leon replied to Keith Browning's topic in Body, Chassis and Electrical
When I said the pressures were super high, they were at 380 high side and 175 low side this was a couple of minutes after it quit working when I was verifying the concern. These were the pressures in the system without it operating. Then I evacuated and recharged. since then its working normally. -
2017 F-Series 6.7L A/C Not Cooling
leon replied to Keith Browning's topic in Body, Chassis and Electrical
True, on that Keith. I cannot tell you how much air was in the system. I just know that our machine purged air for a long period of time after recovery (much longer than normally experienced). I recharged a bit less than the spec. just to operate the system to see if pressures went high again. The pressures were at 225 high side and 36 low side at 93 degrees with 80% humidity in the shop. the air flow from the center vents was normal and 44 f. I operated it a couple of times with about 30 minutes rest in between. and both times it worked normally. I appreciate the heads up on the wire issue, and yes there is a message or bulletin on that. I will open that wiring convolute up and verify the circuits...the wire ties appear to really be tight on the loom. -
2017 F-Series 6.7L A/C Not Cooling
leon replied to Keith Browning's topic in Body, Chassis and Electrical
Keith I have 2 '17s right now both no cold air both a/c compressor not engaging. the first one I have a multitude of problems, 1 being the ms CAN is down. I also load tested the wires from c1046 to the compressor clutch, they were good, I attempted to power and ground the clutch and it does not engage with my power probe. I also unplugged all the connectors in the rear of the truck looking for water and corrosion, I did't see anything but for some reason my ms CAN came back and hasn't faultered since. I wired in a fog light bulb into the compressor connector and it will light when I turn on the ac, I am waiting on a coil/clutch for it. #2 f550 low and high sides are super high, evacuated and got 1lb. 12 oz. and a shit ton of air. recharged at 1, 8. and am monitoring the system for operation, it is very cold at center vent 44 degrees. blower works on all speeds. system seems right. just not sure why I had air in the system. air flow from vents feels normal at all speeds. -
Thanks, Chad. I think my problem on finding information on this was I was lookling for des.and op. of a level/heater assembly For some reason I couldn't grasp the reductant quality module as being my target... I guess... I suppose its time to revisit the pced and enjoy some quality reading.
-
Ok guys, I was on this same thought path, but I was having a hard time making sure. It seems to reason to me that its most likely the way it is going to operate. Keith I was looking through that section and...well I didn't see what I was looking for. I'm sure you are right. thanks for the replies
-
I am trying to find information on the operation of this gauge, customer complains of gauge drops from full to @ half with no indication in between it came in reading @ half and I put in 2 gallons and it is reading full. No codes in ipc. I'm not sure what type of level sender it is using, And I can't seem to find what I'm looking for in the wsm or pced.
-
I'm betting on you have a egr cooler starting to leak. Even though it holds vacuum I've been through similar scenarios before and 9/10 the cooler would let go in less than a 1000 miles. That being said you still need an egr valve and a turbo cleaning.
-
I performed 16b24 on a dpf deleted truck.
leon replied to leon's topic in 6.7L Power Stroke® Diesel Engines
It was on the repair order but not on the write up, the customer is weighing his options. I think I could work around this if I had another programmed truck with the programmer but our used up car department might inherit this. -
I performed 16b24 on a dpf deleted truck.
leon replied to leon's topic in 6.7L Power Stroke® Diesel Engines
Thanks guys for the moral support. I have caught many of the reprograms over the years and have given the customer the opportunity to give the yes/no, but I just got upside down here and obviously am rushing myself to get things done. -
I have a truck in here it is a 11 550, it has multiple problems to diag, but it also had the 16b24. I have no excuses for my mental lapse but right now I have a lot of stuff going on here and at home. I was trying to be efficient about things and while I was performing a prior approval on a def heater for another truck I thought I would at least get the 16b24 done. About 3/4 of the way through it hit me that the dpf had been deleted. customer just bought this truck 6 months ago in a different state and doesn't have the programmer. Well, I feel like a real idiot right now and short of putting all the ex. components back on, (which he doesn't have either), I will probably end up buying a dpf delete programmer. I have to look at costs here so I am asking if anyone has a cost effective programmer or alternative ideas?
-
Right side up-pipe removal tricks???
leon replied to Mekanik's topic in 6.4L Power Stroke® Diesel Engines
what is a legitimate time to charge out on these under cp? if I read the slts correctly it is 6.3 warr. time is that correct? -
keith, thanks, I did see that and what I eventually found was at the dlc the boom rig is connected to the dlc and the wiring from the upfitting is a little "rough" . found a strand of wire sticking out from loom and making connection with another the wires were stipped back quite a way and I tried to remove and heat shrink over them for the repair but they were too large to fit back into the connector...taped the hell out of it, has been gone for a while now
-
08 f550, u0073 in pcm, I remember reading on a post either here or on PTS that some people were finding a wire chafe around the radiator area, can someone enlighten me as the specifics? Ive checked tbc and rcm wiring, this is an intermittant problem. this has a stellar boom on it and I have checked the wiring at dlc for issues and do not see any problems, my arms and hands are tired from wiggling and yanking on harnesses!!!!
-
keith, I too have had a few 7.3l with a rough idle caused by sloppy d.m. flywheel but this one was nothing I mean nothing at all similar to those. Also how does the engine run with the sync pid at no? Thanks for your input
-
ok, I feel compelled to let anyone interested know what fixed this one. first off, late build 04 with a 6speed 4x4, at times at start it will run verrry slow (150-300 rpm's) when this happens synch pid goes to no ficm synch yes, and yes it is still running, do not loose cam or crank sensor to pcm I swapped both cam and crank sensors with another truck no difference, overlayed wiring from both sensors to pcm again no difference, attempted to move crank trigger wheel...no movement tried a different pcm and ficm..does anyone see the desperation in this yet? thank goodness for a donor truck that was available during this trucks 4week stay. multiple calls to hotline and fse visited for one day all of us were still scratching our noggins. then...one time while it was doing this I was playing with the ignition witch and the starter engaged for a moment while it was running, and BAM! it came out of its fit. I was able to do this every time. this truck had a dual mass flywheel and at times on start it would do some sort of crazy resonance shit to the crank and cause it to loose sync a single mass flywheel and clutch fixed it... that should have been my first thought, what a moron!
-
thank you, it seems like I am always running into something a little different on these things. I am ready for some straight forward repairs for a while at least.
-
ok same truck, when this happens it runs on 3-4 cyls, really struggles to keep idling, cannot perform power balance test when this happens, also found a very strange pid condition, synch pid will read no but ficm synch will read yes, wtf? have swapped pcm and ficm and it still occurs, ficm voltages are normal when this occurs. this one is starting to get to my head!!
-
it is a late build (icp and connector have been changed also ipr valve, (hotline recommended)
-
icp stars at .24v and goes to 1.06 when this happens (800psi) builds within 1.5 seconds
-
I have a 04 f250 that when starting sometimes, the engine rpm's slowly go up to idle speed. other times when it stars "normally" rps ramp up and then go down to idle speed, (I hope that makes sense). There are no cmdtc's or on demand codes, engine seems to run normally and this may happen warm or cold, when monitoring pids found that ipr commanded when this happens is less than 40% during crank mode. when it starts normally it goes over 75%. monitored ficm synch, rpm, icp, ipr vpwr, vref, and cannot come to any conclusion, changed to 10/30 rotunda still does it, any ideas? this is one I havent seenbefor it has 70k on odometer and looks pretty well taken care of.
-
this is a ford reman and I assumed responsibility as soon as I opened the hood, (powertrain warranty). Have had contact with ford hotline and had our fse look at it, we are putting new (commonized) heads on as there is no valve train clearance on #1 and only .002 on #2, valves are recessed in head about .030 and pass side engine deck has been machined, not sure how much, but will let you guys know what happens, thanks ktmlew for reading this post carefully I know it is difficult to follow.
-
I am working on a 03 f250, I installed reman long block, as soon as I started spinning it over I could tell that there was a compression problem with a cyl. found #1 cylinder intake valves leaking air, no obvious problems were noticed with valve covers off, swapped push rods with another cyl and compression was up higher but still 100 psi below others (280 vs 375-390), as I was removing cyl head I was running leakdown tester while I backed off head bolt and rocker carrier bolts and the air leak stopped, comepletely. removed head and replaced lifters on #1 cyl reassemble and same thing. the next test was to measure total clearance between rocker and crossbar with the lifter collapsed of coarse #1 intake had no clearance but others (did all 16) ranged from .002 to .040, ok my question is what clearance would you be comfortable with? my thinking is that if this was a mechanical grind cam that I would need a min of .015 I am looking for any input on this sublect. thanks
-
well, I got the job, replaced all 8, the truck was sold under the condition that it started cold, and it worked perfectly, thanks for all the input. on to the next one (so many trucks so little time)